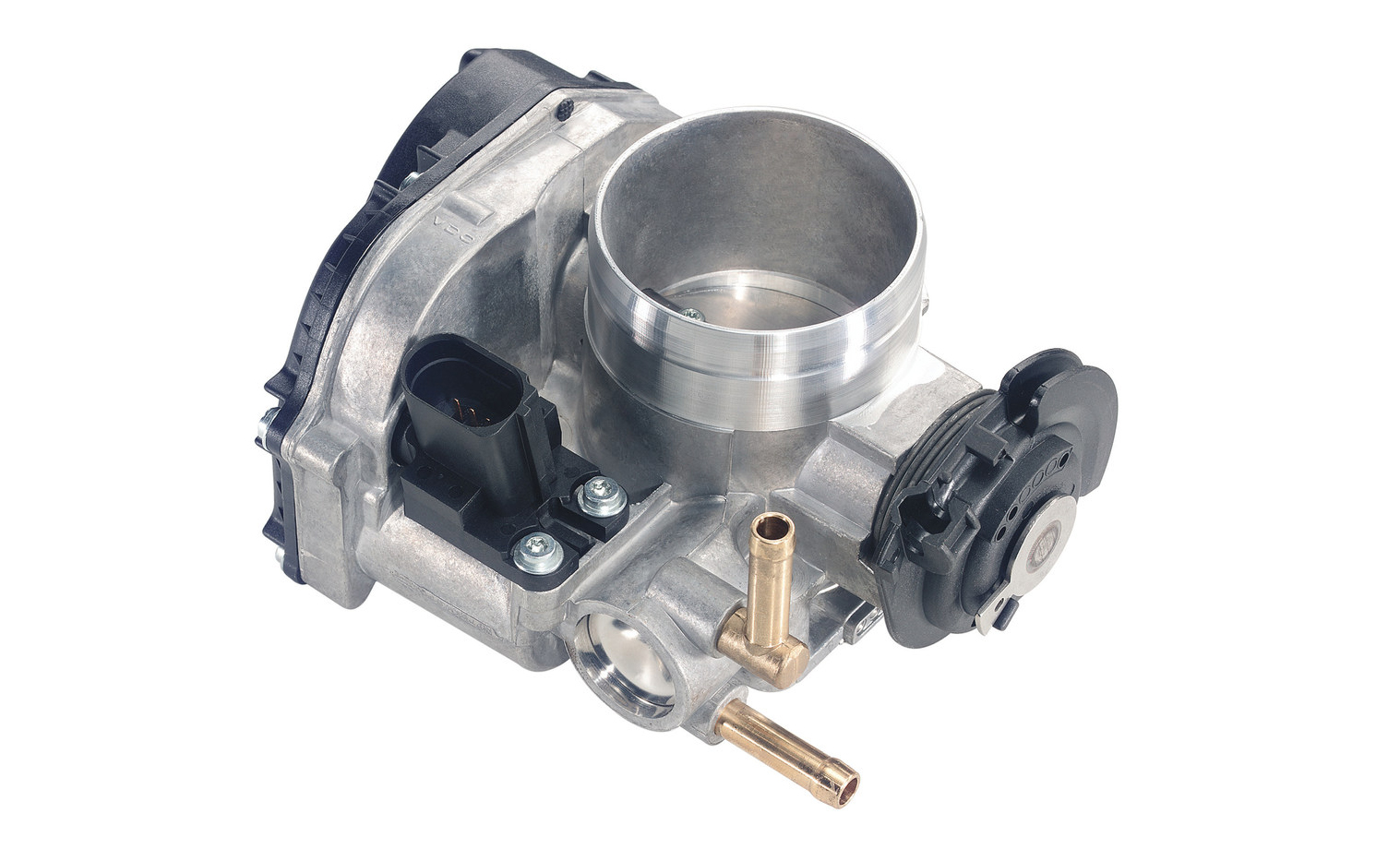
Our engine actuators ensure optimum utilisation of the potential of modern engine management systems and offer consistently high performance. The fuel must be prepared for combustion, i.e. mixed with air. The fuel-air mixture is then fed into the combustion chamber of the engine.
The valve angle is monitored by throttle electronics, which remain in constant communication with the engine management system. The resulting data is compared in real-time. The optimum throttle position is calculated by the engine management system with regard to both fuel economy and emissions. The information is then fed back to the throttle electronics, which adjust the throttle angle accordingly.
The engine management system compares the position of the accelerator with other on-board sensor data. The optimum throttle angle is then calculated based on current engine conditions. This data is sent to the throttle and the valve is positioned accordingly, i.e. the throttle is controlled solely by means of an electronic signal from the engine management system. Key benefits include improved efficiency under all load conditions.
Idle-speed controllers provide dynamic adjustment of airflow in the throttle bypass valve, ensuring optimal idling at all times. Working in conjunction with the corresponding sensors and an electronic control unit, these devices provide a rapid response to any variation in idle speed.
Digital linear actuators provide incremental adjustment of airflow in the throttle bypass valve, ensuring optimal idling at all times. These devices provide a quick response to any variation in idle speed, working in conjunction with the corresponding sensors.
The electric actuator with integrated position sensor and optional integrated electronics allows intake manifold throttles or turbo charge guide vanes for example to be continuously adjusted. Its more precise control means that it is taking the place of standard pneumatic drives which can no longer satisfy the more stringent requirements.
Compared with traditional valves, the electrically actuated exhaust recirculation valves enable even more accurate control of the exhaust recirculation rates in Diesel engines and direct injection gasoline engines. This way they make an important contribution towards meeting ever stricter exhaust emission standards.
Continental Sensors and Motors e.g. for the Valvetronic System
With help of the Valvetronic System the vehicle power is more direct and increased. On the other hand the consumption is reduced by up to 10% within the gasoline engine. Within this system the airflow is controlled by the Variable Valve Lift and replaces the Throttle Valve. Nevertheless, a Throttle Valve is still mounted and responsible for other functionalities like emergency operation.
The high-precision Continental Motors adjust continuously the eccentric shaft of the system. Via the eccentric shaft and the cam shaft driven rocker arm the intake valves are variably adjusted. The VDO Sensors exactly control the adjusted angle of the eccentric shaft and report this value to the engine management.
Variable valve timing (VVT) solenoid valves control the camshaft through changes in oil pressure, enabling them to regulate the engine in a variable manner. The advantages are optimized filling of cylinders and improved engine performance over different engine speeds. Engine emissions are also reduced.
Our electric water pumps with integrated control unit ensure reliable, precise and demand-controlled engine cooling.
OE-Quality with respect to accurate fit, functionality, service life, reliability and safety
Use the Online Catalog service to get more details about this product which can be installed in your vehicle (passenger car).
Our engine actuators ensure optimum utilisation of the potential of modern engine management systems and offer consistently high performance. The fuel must be prepared for combustion, i.e. mixed with air. The fuel-air mixture is then fed into the combustion chamber of the engine.
The valve angle is monitored by throttle electronics, which remain in constant communication with the engine management system. The resulting data is compared in real-time. The optimum throttle position is calculated by the engine management system with regard to both fuel economy and emissions. The information is then fed back to the throttle electronics, which adjust the throttle angle accordingly.
The engine management system compares the position of the accelerator with other on-board sensor data. The optimum throttle angle is then calculated based on current engine conditions. This data is sent to the throttle and the valve is positioned accordingly, i.e. the throttle is controlled solely by means of an electronic signal from the engine management system. Key benefits include improved efficiency under all load conditions.
Idle-speed controllers provide dynamic adjustment of airflow in the throttle bypass valve, ensuring optimal idling at all times. Working in conjunction with the corresponding sensors and an electronic control unit, these devices provide a rapid response to any variation in idle speed.
Digital linear actuators provide incremental adjustment of airflow in the throttle bypass valve, ensuring optimal idling at all times. These devices provide a quick response to any variation in idle speed, working in conjunction with the corresponding sensors.
The electric actuator with integrated position sensor and optional integrated electronics allows intake manifold throttles or turbo charge guide vanes for example to be continuously adjusted. Its more precise control means that it is taking the place of standard pneumatic drives which can no longer satisfy the more stringent requirements.
Compared with traditional valves, the electrically actuated exhaust recirculation valves enable even more accurate control of the exhaust recirculation rates in Diesel engines and direct injection gasoline engines. This way they make an important contribution towards meeting ever stricter exhaust emission standards.
Continental Sensors and Motors e.g. for the Valvetronic System
With help of the Valvetronic System the vehicle power is more direct and increased. On the other hand the consumption is reduced by up to 10% within the gasoline engine. Within this system the airflow is controlled by the Variable Valve Lift and replaces the Throttle Valve. Nevertheless, a Throttle Valve is still mounted and responsible for other functionalities like emergency operation.
The high-precision Continental Motors adjust continuously the eccentric shaft of the system. Via the eccentric shaft and the cam shaft driven rocker arm the intake valves are variably adjusted. The VDO Sensors exactly control the adjusted angle of the eccentric shaft and report this value to the engine management.
Variable valve timing (VVT) solenoid valves control the camshaft through changes in oil pressure, enabling them to regulate the engine in a variable manner. The advantages are optimized filling of cylinders and improved engine performance over different engine speeds. Engine emissions are also reduced.
Our electric water pumps with integrated control unit ensure reliable, precise and demand-controlled engine cooling.
OE-Quality with respect to accurate fit, functionality, service life, reliability and safety
Use the Online Catalog service to get more details about this product which can be installed in your vehicle (passenger car).